SINGLE DRIVE HIGH PRESSURE GRINDING ROLL
Application Scope
Single-drive high pressure grinding roll is specially designed to pre-grind the cement clinkers, the mineral dross, the steel clinkers and so on into small granules, to ultra-crush the metallic minerals (iron ores, manga- nese ores, copper ores, lead-zinc ores, vanadium ores and others) and to grind the non-metallic minerals (the coal gangues,
feldspar, nephe- line, dolomite, limestone, quartz, etc.) into powder .
Structure & Working Principle
◆Working Principle Diagram
The singledrive high pressure grinding roll adopts
the grinding principle of material aggregate extrusion .
One is stationary roll and the other is movable roll.
The two rolls rotate oppositely at the same speed .
The materials enter from the upper feed opening,
and are grinded due to extrusion by high pressure in the gap of the two rolls, and discharged from the bottom .
◆Drive part
Only one motor drive is needed,
the power is transmitted from the stationary roll to the movable roll through the gear system,
so that the two rolls are fully synchronized with no sliding friction .
The work is all used for material extrusion,
and the energy consumption utilization rate is high, which saves 45% of electricity compared to conventional high pressure grinding roll .
◆Pressure applying system
The combined spring mechanical pressure applying system makes the movable roll avoid flexibly .
When there is iron foreign matter entering,
the spring pressure applying system directly sets back and reacts in time, ensuring the operation rate is as high as 95%;
while the traditional high pressure grinding roll makes avoiding, the hydraulic oil needs to be discharged through the pipeline for pressure relief .
The action is delayed, which may cause damage to the roll surface or malfunction of the hydraulic system .
◆Roll surface
The roll surface is surfacing welded with alloy wear-resistant welding material, and the hardness can reach HRC58-65; the pressure is automatically adjusted with the material,
which not only achieves the purpose of grinding, but also protects the roll surface;
the movable roll and the stationary roll operate synchronously without sliding friction.
Therefore, the service life of the roll surface is much higher than that of the conventional high pressure grinding roll .
Main Technical Features
◆ High Working Efficiency. Compared with the traditional crushing equipment, the processing capacity increases by 40 - 50% .
The processing capacity for PGM1040 can reach around 50 - 100 t/h, with only 90kw power .
◆ Low Energy Consumption . As per the single roll driving way, it needs only one motor to drive .
The energy consumption is very low. Compared with the traditional double drive HPGR, it can reduce the energy consumption by 20~30% .
◆ Good Wear-resistant Quality . With only one motor driving, the synchronization performance of the two rolls is very good .
With wear-resistant welding surfaces, the rolls are with good wear-resistant quality and can be easily maintained .
◆ High Operation Rate: ≥ 95%. With scientific design, the equipment can be pressurized by the high pressure spring group .
The working pressure can be adjusted automatically as per the spring group compress. There is no malfunction point .
◆ High Automation and easy adjustment . Without the hydraulic system, there is low malfunction rate
◆ The roll surface is surfacing welded with alloy wear-resistant welding material, with high hardness and good wear-resistance;
The pressure to the spring comes from the reaction force of the material, and the pressure is always balanced,
which not only achieves the purpose of crushing,
but also protects the roll surface; the movable roll and the stationary roll are meshed and driven by the gear system,
and the speed is completely synchronized, thereby avoiding sliding friction between the material and the roll surface.
Therefore, the service life is much higher than that of the double drive HPGR .
◆ Compact structure and small floor space .
Technical Parameters
Model | Roll diametermm | Roll widthmm | M ax .feedsize (Cement,steel slag, oreslag) mm | Optimum feedsize (metallicm i n e r a l ,non-metallicmineral) mm | mmOutput size(cement) mm | ProcessingcapacityT/h | M o t o rpower Kw | Outline dimensions(L×W×H)mm |
PGM0850 | φ800 | 500 | 50 | 30 | Classifying,< 4 | 30 ~ 40 | 37 | 2760×2465×1362 |
PGM1040 | φ1000 | 400 | 50 | 30 | Classifying,< 4 | 50 ~ 80 | 90 | 4685×4300×2020 |
PGM1060 | φ1000 | 600 | 50 | 30 | Classifying,< 4 | 70 ~ 110 | 110 | 4685×4300×2020 |
PGM1065 | φ1000 | 650 | 50 | 30 | lassifying,< 4 | 100 ~ 160 | 200 | 5560×4500×2200 |
PGM1250 | φ1200 | 500 | 50 | 30 | Classifying,< 4 | 120 ~ 180 | 250 | 6485×4700×2485 |
PGM1465 | φ1400 | 650 | 50 | 30 | Classifying,< 4 | 240 ~ 320 | 630 | 9200×6320×3600 |
PGM1610 | φ1600 | 1000 | 50 | 30 | Classifying,< 4 | 500 ~ 650 | 1250 | 10800×8100×4400 |
COMPARISON BETWEEN SINGLE DRIVE HPGR AND CONVENTIONAL HPGR
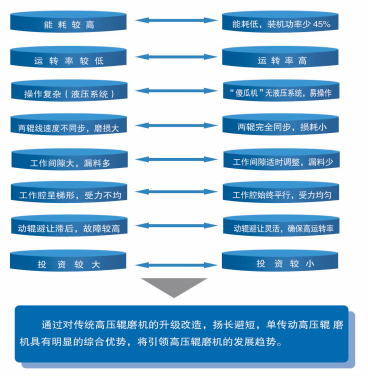
PRE-GRINDING PROCESS FLOW CHART OF SINGLE DRIVE HPGR
Pre-grinding of cement, ore slag and steel slag “More crushing and less grinding, replace grinding with crushing”, that is, pre-grinding, has become the mainstream technology for pipe mill production process to increase production and reduce energy consump- tion . As the most advanced pre-grinding energy-saving equipment, single-drive HPGR can crush the materials to -4mm or -0 .5mm, of which 0 .08mm accounts for more than 30% . The capacity of utilized ball mill can be increased by 50~100%, and the system grinding power consumption can be reduced by 15~30% .
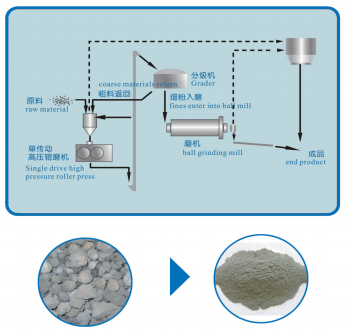
ULTRA FINE CRUSHING PROCESS FLOW CHART OF METALLIC MINERAL WITH SINGLE DRIVE HPGR
Ultra Fine Crushing of Metallic Mineral
When the minerals pass through the gap between the two rolls, they are crushed into fine particles of -5 mm or -3 mm and a large amount of powder by high pressure force . Due to the weak bonding force of the interface between the useful mineral and the gangue, fatigue fracture or micro-crack and internal stress are easily generated. Part of the interface will be completely dissociated .
Due to the high content of fine powder discharged from the HPGR and the fact that the minerals are crushed along the dissociation surface, compared with the con- ventional crushing, the proportion of intergrowth in the crushed products is reduced, and the tailing discard ef- fect is good .
Both the coarse concentrate grade and the waste discard yield are greatly improved .
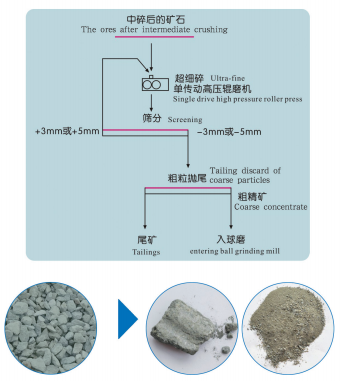
APPLICATION PROCESS FLOW CHART FOR NON-METALLIC MINERAL WITH SINGLE DRIVE HPGR
Non-Metallic Mineral Grinding
Compared with traditional grinding equipment, sin- gle-drive HPGR has the advantages of large single ma- chine capacity, low energy consumption, less wear and less iron pollution; the product fineness can be controlled from 20 mesh to 120 mesh, which can replace ball mill and create a new grinding process .
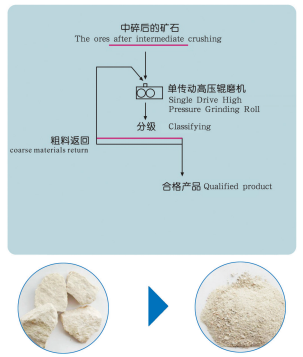
HPGM SERIES HIGH PRESSURE GRINDING ROLL
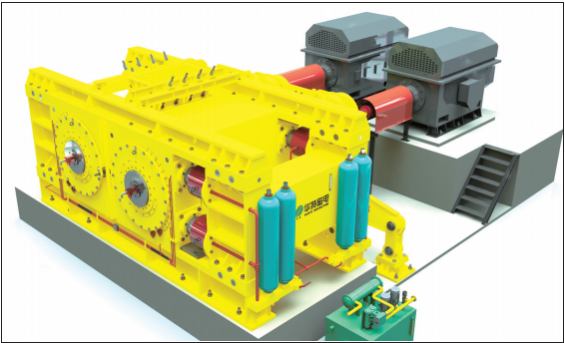
Working Principle
HPGM series high pressure grinding roll is a new type of energy-saving grinding equipment designed by the principle of high-pressure material layer pulverization . It consists of two squeezing rolls that rotate synchronously at a low speed . One is a stationary roll and the other is a movable roll, which are both driven by a high-power motor. The materials are evenly fed from above the two rolls, and are continuously carried into the roll gap by the squeezing roll. After being subjected to a high pressure of 50-300 MPa, the dense material cake is discharged from the machine . In the discharged material cake, in addition to a certain proportion of the qualified products, the internal structure of the particles of non- qualified products is filled with a large number of micro cracks due to high pressure extrusion, so that the material’s grind ability is greatly improved . For the materials after extrusion, after breaking up, classifying and screening, the fine materials of less than 0.8 mm can reach about 30%, and the materials of less than 5 mm can reach more than 80% . There- fore, in the further grinding process, the grinding energy consumption can be reduced to a large extent, so that the production capacity of the grinding equipment can be fully exerted, generally the ball mill system capacity can be increased by 20%~50%, and the total energy consumption can be reduced by 30%~50% or more .
Application Fields
There are many kinds of metal ore resources in China, but the qualities of most mineral varieties are poor, miscella- neous and fine . In order to solve the outstanding problems in the economic, technical and environmental protection aspects of mining development, domestic metal mining enterprises actively introduce, digest and absorb foreign new and efficient mining production equipment . In this market background, the HPGR is high-efficiency grinding equipment first researched and demonstrated, and begins to be used in domestic metal mining enterprises . It is also the mine production equipment most concerned by the domestic mining industry . It can be said that HPGR is widely used in domestic metal mines . The HPGR has been widely used home and abroad in the grinding in the cement industry, granulation in the chemical industry, and fine grinding of pellet to increase the specific surface area . It is used for the crushing of metal ore to achieve dif- ferent purposes such as simplifying the crushing process, more crushing and less grinding, improving system productivity, improving grinding effect or separation indicators .
Practical Application Scope
1. Medium, fine and ultrafine grinding of bulk materials .
2. In the mineral processing industry, can be placed before the ball mill, as a pre-grinding equipment, or make up a combined grinding system with a ball mill .
3. In the oxidized pellet industry, can replace the commonly used damp mill .
4.In building materials, refractory materials and other industries, have been successfully applied in cement clinker, limestone, bauxite and other grinding .
Product Advantages
1. Constant pressure design ensures smooth pressure between rolls and ensures crushing effect .
2. Automatic deviation correction, can quickly adjust the roll gap to ensure the smoothness of the equipment .
3. The edge separation system reduces the effect of edge effects on the crushing effect .
4. With cemented carbide studs, long service life, easy maintenance, and replaceable .
5. The valve bank adopts imported components, and the hydraulic system has reasonable design and good reliability .
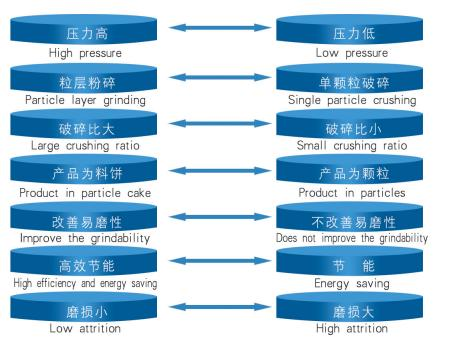
Structure of HPGR
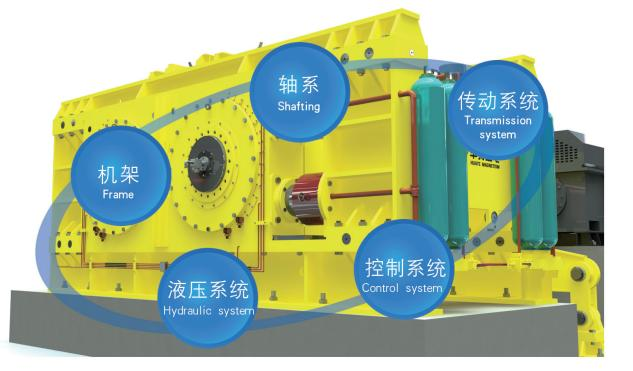
Model | Roll diametermm | Roll width mm | Throughputcapacity | Feed size | Machine weightt | Installed power |
HPGM0630 | 600 | 300 | 25-40 | 10-30 | 6 | 74 |
HPGM0850 | 800 | 500 | 50-110 | 20-35 | 25 | 150-220 |
HPGM1050 | 1000 | 500 | 90-200 | 20-35 | 52 | 260-400 |
HPGM1250 | 1200 | 500 | 170-300 | 20-35 | 75 | 500-640 |
HPGM1260 | 1200 | 600 | 200-400 | 20-35 | 78 | 600-800 |
HPGM1450 | 1400 | 500 | 200-400 | 30-40 | 168 | 600-800 |
HPGM1480 | 1400 | 800 | 270-630 | 30-40 | 172 | 800-1260 |
HPGM16100 | 1600 | 1000 | 470-1000 | 30-50 | 220 | 1400-2000 |
HPGM16120 | 1600 | 1200 | 570-1120 | 30-50 | 230 | 1600-2240 |
HPGM16140 | 1600 | 1400 | 700-1250 | 30-50 | 240 | 2000-2500 |
HPGM18100 | 1800 | 1000 | 540-1120 | 30-60 | 225 | 1600-2240 |
HPGM18160 | 1800 | 1600 | 840-1600 | 30-60 | 320 | 2500-3200 |
New type stud roll surface technology
It adopts high-quality hard alloy studs with high hardness and good wear resistance .
The stud arrangement is designed by computer simulation,
and the arrangement is reasonable, which can form a uniform material layer between the studs, effectively protecting the studs and roll surfaces,
and improving the ser vice life of squeezing roll . The studs are installed with imported special adhesives for easy replacement .
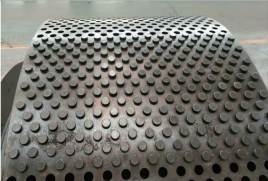
Separation technology of roll bush- ing and main shaft
The main body of the squeezing roll is made of high-quality forged steel, and the roll bushing is forged with high-quality alloy steel . The main shaft and the rolls are made of different materials, which improves the toughness of the main shaft and the rigidity of the roll bushing . The service life of the shaft bushing is greatly improved . The replacement of the roll bushing is convenient .
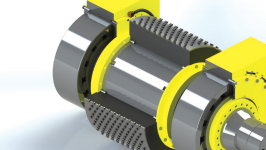
Bearing quick mounting and dis- mounting technology High-quality tapered hole bearings are adopted and high- pressure oil tank is preformed . The bearing can be easily dismounted through high-pressure oil pump, greatly reducing the difficulty of replacing the bearing and improving the maintenance efficiency
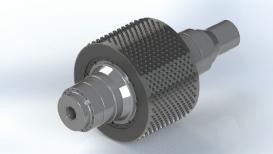
Multiple combined sealing technology
The bearing seal adopts a variety of J-type plus V-type and labyrinth seals, and the combined sealing technology effectively ensures the sealing effect of the bearing .
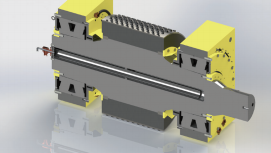
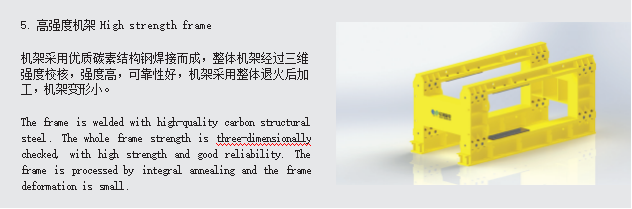
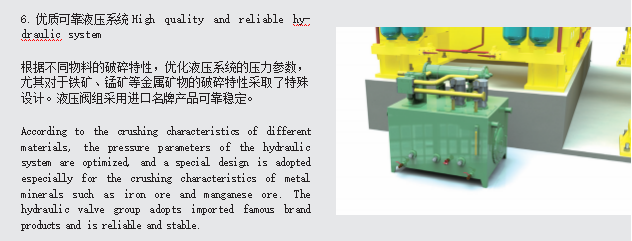
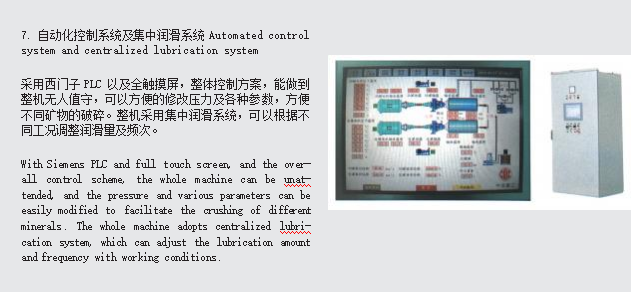
Iron Ore Beneficiation Flow
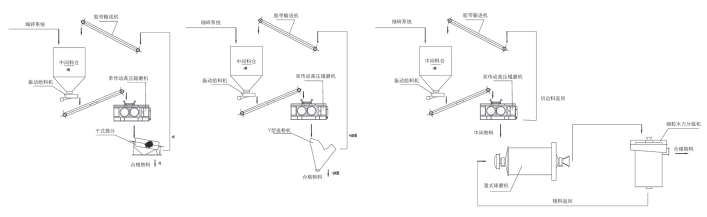
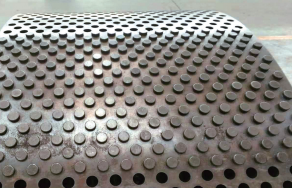
High Quality Wear-Resistant Roll Surface with Studs
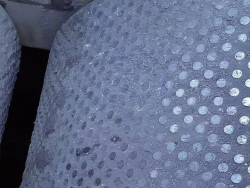
After the materials are extruded,
a dense material layer is formed on the roll surface to protect the roll surface .
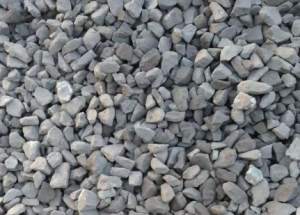
Raw Material
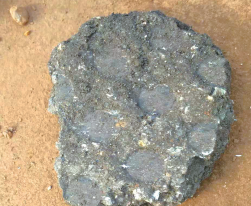
Material Cake