With special physical and chemical properties, kaolin is an indispensable nonmetallic mineral resource in ceramics, paper making, rubber, plastics, refractories, petroleum refining and other industrial and agricultural and national defense cutting-edge technology fields. The whiteness of kaolin is an important indicator of its application value.
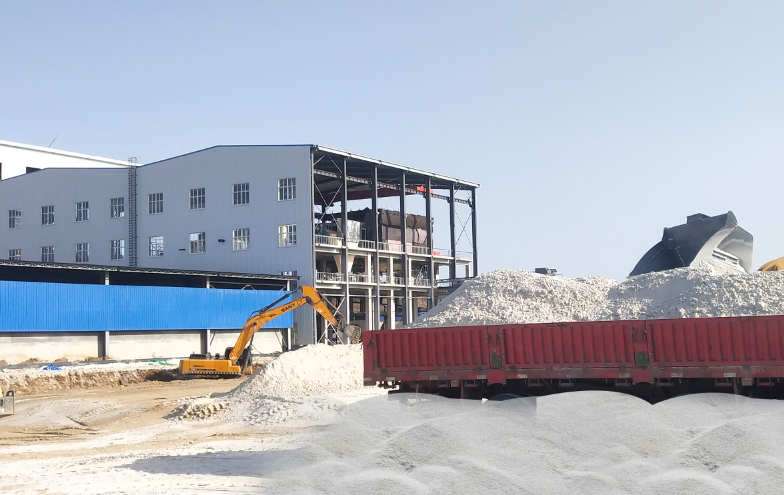
Factors affecting the whiteness of kaolin
Kaolin is a kind of fine-grained clay or clay rock mainly composed of kaolinite minerals. Its crystal chemical formula is 2SiO2 · Al2O3 · 2H2O. A small amount of non-clay minerals are quartz, feldspar, iron minerals, titanium, aluminum hydroxide and oxides, organic matter, etc.
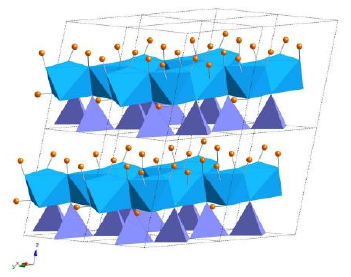
Crystalline structure of kaolin
According to the state and nature of impurities in kaolin, the impurities that cause the decrease of whiteness of kaolin can be divided into three categories: organic carbon; Pigment elements, such as Fe, Ti, V, Cr, Cu, Mn, etc; Dark minerals, such as biotite, chlorite, etc. Generally, the content of V, Cr, Cu, Mn and other elements in kaolin is small, which has little effect on whiteness. The mineral composition and content of iron and titanium are the main factors affecting the whiteness of kaolin. Their existence will not only affect the natural whiteness of kaolin, but also affect its calcined whiteness. In particular, the presence of iron oxide has a negative impact on the color of clay and reduces its brightness and fire resistance. And even if the amount of oxide, hydroxide and hydrated oxide of iron oxide is 0.4%, it is enough to give the clay sediment red to yellow coloring. These iron oxides and hydroxides can be hematite (red), maghemite (red-brown), goethite (brownish yellow), limonite (orange), hydrated iron oxide (brownish red), etc. It can be said that the removal of iron impurities in kaolin plays an extremely important role in the better use of kaolin.
Occurrence state of iron element
The occurrence state of iron in kaolin is the main factor determining the method of iron removal. A large number of studies believe that crystalline iron in the form of fine particles is mixed in kaolin, while amorphous iron is coated on the surface of fine particles of kaolin. At present, the occurrence state of iron in kaolin is divided into two types at home and abroad: one is in kaolinite and accessory minerals (such as mica, titanium dioxide and illite), which is called structural iron; The other is in the form of independent iron minerals, called free iron (including surface iron, fine-grained crystalline iron and amorphous iron).
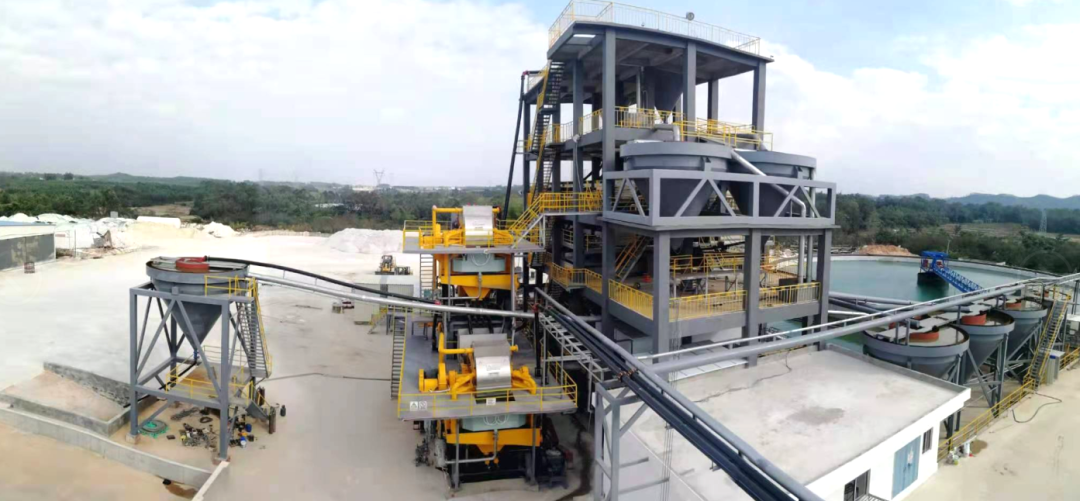
The iron removed by iron removal and whitening of kaolin is free iron, mainly including magnetite, hematite, limonite, siderite, pyrite, ilmenite, jarosite and other minerals; Most iron exists in the form of highly dispersed colloidal limonite, and a small amount in the form of spherical, acicular and irregular goethite and hematite.
Iron removal and whitening method of kaolin
Water separation
This method is mainly used to remove detrital minerals such as quartz, feldspar and mica, and coarser impurities such as rock debris, as well as some iron and titanium minerals. Impurity minerals with similar density and solubility to kaolin can not be removed, and the whiteness improvement is relatively not obvious, which is suitable for beneficiation and whitening of relatively high-quality kaolin ore.
Magnetic separation
Iron mineral impurities in kaolin are usually weak magnetic. At present, the high gradient strong magnetic separation method is mainly used, or the weak magnetic minerals are converted into strong magnetic iron oxide after roasting, and then removed by ordinary magnetic separation method.
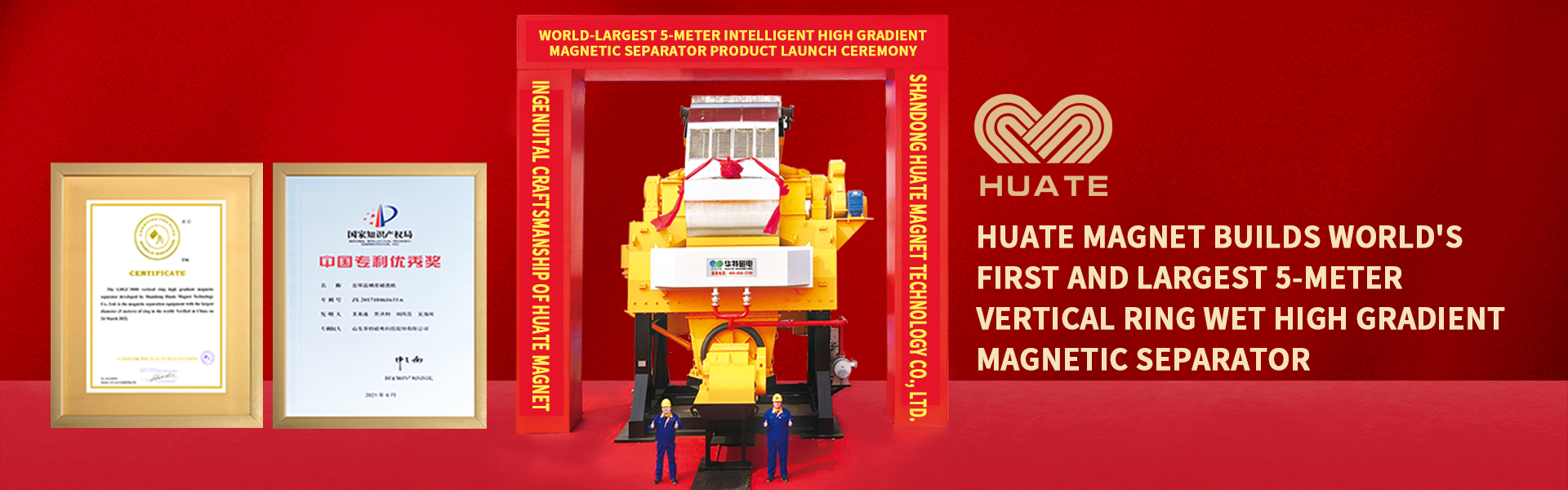
Vertical ring high gradient magnetic separator
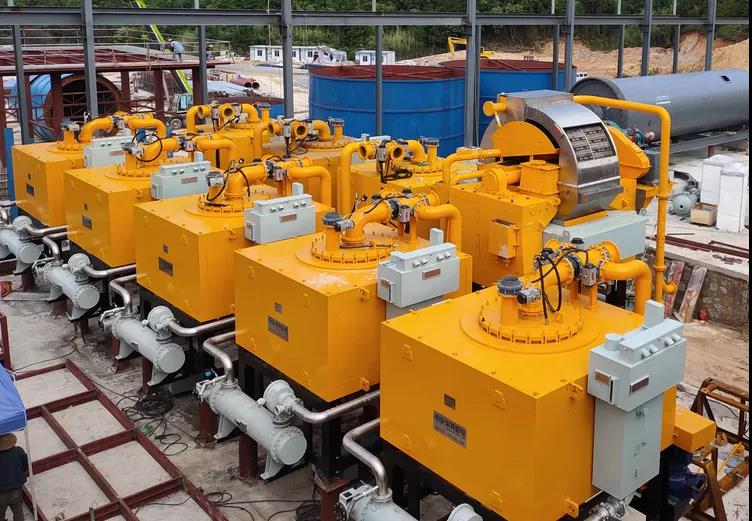
High gradient magnetic separator for electromagnetic slurry
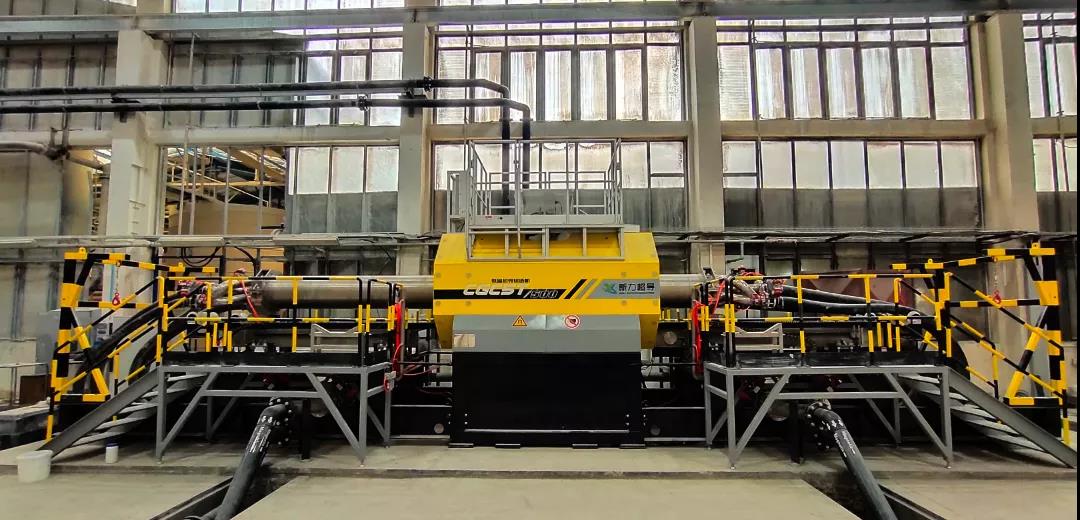
Low temperature superconducting magnetic separator
Flotation method
The flotation method has been applied to treat kaolin from primary and secondary deposits. In the flotation process, kaolinite and mica particles are separated, and the purified products are several suitable industrial grade raw materials. The selective flotation separation of kaolinite and feldspar is usually carried out in the slurry with controlled pH.
Reduction method
The reduction method is to use a reducing agent to reduce the iron impurities (such as hematite and limonite) in the trivalent state of kaolin to soluble bivalent iron ions, which are removed by filtration and washing. The removal of Fe3+impurities from industrial kaolin is usually achieved by combining physical technology (magnetic separation, selective flocculation) and chemical treatment under acidic or reducing conditions.
Sodium hydrosulfite (Na2S2O4), also known as sodium hydrosulfite, is effective in reducing and leaching iron from kaolin, and is currently used in kaolin industry. However, this method must be carried out under strong acidic conditions (pH<3), resulting in high operating costs and environmental impact. In addition, the chemical properties of sodium hydrosulfite are unstable, requiring special and expensive storage and transportation arrangements.
Thiourea dioxide: (NH2) 2CSO2, TD) is a strong reducing agent, which has the advantages of strong reducing ability, environmental friendliness, low decomposition rate, safety and low cost of batch production. Insoluble Fe3+in kaolin can be reduced to soluble Fe2+through TD.
Subsequently, the whiteness of kaolin can be increased after filtration and washing. TD is very stable at room temperature and neutral conditions. The strong reduction ability of TD can only be obtained under the conditions of strong alkalinity (pH>10) or heating (T>70 ° C), resulting in high operation cost and difficulty.
Oxidation method
Oxidation treatment includes the use of ozone, hydrogen peroxide, potassium permanganate and sodium hypochlorite to remove the adsorbed carbon layer to improve whiteness. The kaolin in the deeper place under the thicker overburden is gray, and the iron in the kaolin is in the reducing state. Use strong oxidizing agents such as ozone or sodium hypochlorite to oxidize insoluble FeS2 in pyrite to soluble Fe2+, and then wash to remove Fe2+from the system.
Acid leaching method
The acid leaching method is to transform the insoluble iron impurities in kaolin into soluble substances in acidic solutions (hydrochloric acid, sulfuric acid, oxalic acid, etc.), thus realizing the separation from kaolin. Compared with other organic acids, oxalic acid is considered to be the most promising because of its acid strength, good complexing property and high reducing ability. With oxalic acid, the dissolved iron can be precipitated from the leaching solution in the form of ferrous oxalate, and can be further processed to form pure hematite through calcination. Oxalic acid can be obtained cheaply from other industrial processes, and in the firing stage of ceramic manufacturing, any residual oxalate in the treated material will be decomposed into carbon dioxide. Many researchers have studied the results of dissolving iron oxide with oxalic acid.
High temperature calcination method
Calcination is the process of producing special grade kaolin products. According to the treatment temperature, two different grades of calcined kaolin are produced. Calcination in the temperature range of 650-700 ℃ removes the structural hydroxyl group, and the escaping water vapor enhances the elasticity and opacity of kaolin, which is an ideal attribute of paper coating application. In addition, by heating kaolin at 1000-1050 ℃, it can not only increase abradability, but also obtain 92-95% whiteness.
Chlorination calcination
Iron and titanium were removed from clay minerals, especially kaolin by chlorination, and good results were obtained. In the process of chlorination and calcination, at high temperature (700 ℃ - 1000 ℃), kaolinite has undergone dehydroxylation to form metakaolinite, and at higher temperature, spinel and mullite phases are formed. These transformations increase the hydrophobicity, hardness and size of particles through sintering. The minerals treated in this way can be used in many industries, such as paper, PVC, rubber, plastics, adhesives, polishing and toothpaste. The higher hydrophobicity makes these minerals more compatible with organic systems.
Microbiological method
Microbial purification technology of minerals is a relatively new mineral processing subject, including microbial leaching technology and microbial flotation technology. The microbial leaching technology of minerals is an extraction technology that uses the deep interaction between microorganisms and minerals to destroy the crystal lattice of minerals and dissolve the useful components. Oxidized pyrite and other sulfide ores contained in kaolin can be purified by microbial extraction technology. Commonly used microorganisms include Thiobacillus ferrooxidans and Fe-reducing bacteria. The microbiological method has low cost and low environmental pollution, which will not affect the physical and chemical properties of kaolin. It is a new purification and whitening method with development prospects for kaolin minerals.
Summary
The iron removal and whitening treatment of kaolin needs to select the best method according to different color causes and different application objectives, improve the comprehensive whiteness performance of kaolin minerals, and make it have high use value and economic value. The future development trend should be to combine the characteristics of chemical method, physical method and microbiological method organically, so as to give full play to their advantages and restrain their disadvantages and shortcomings, so as to achieve better whitening effect. At the same time, it is also necessary to further study the new mechanism of various impurity removal methods and improve the process to make the iron removal and whitening of kaolin develop in the direction of green, efficient and low carbon.
Post time: Mar-02-2023