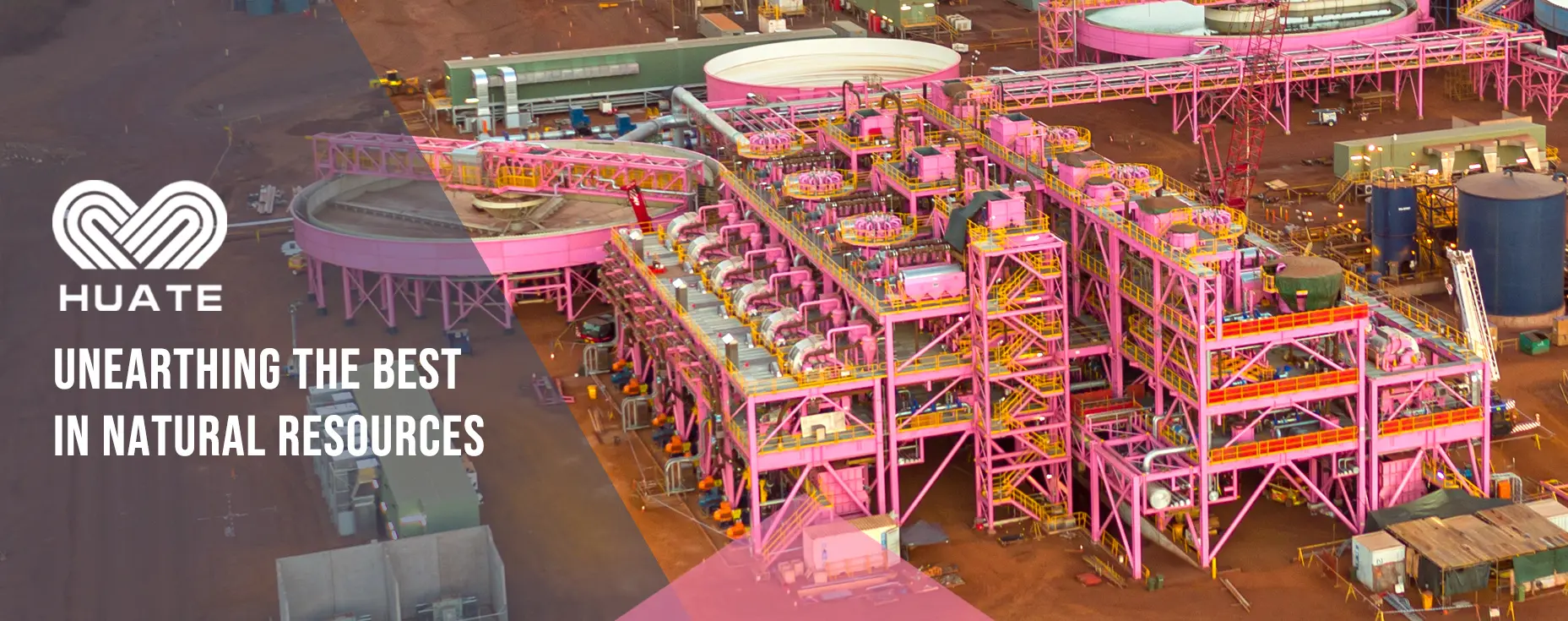
As one of the earliest and most widely used metals in the world, iron ore is an essential raw material for iron and steel production. Currently, iron ore resources are depleting, characterized by a higher proportion of lean ore compared to rich ore, more associated ore, and complex ore compositions. Iron is commonly extracted from its ore, known as hematite or magnetite, through a process called iron ore beneficiation. The specific steps involved in the industrial extraction of iron can vary depending on the nature of the ore and the desired products, but the general process typically involves the following stages:
Mining
Iron ore deposits are first identified through exploration activities. Once a viable deposit is found, the ore is extracted from the ground using mining techniques such as open-pit or underground mining. This initial phase is crucial as it sets the stage for the subsequent extraction processes.
Crushing and Grinding
The extracted ore is then crushed into smaller pieces to facilitate further processing. Crushing is usually done using jaw crushers or cone crushers, and grinding is carried out using autogenous grinding mills or ball mills. This process reduces the ore to a fine powder, making it easier to handle and process in the subsequent stages.
Magnetic Separation
Iron ore often contains impurities or other minerals that need to be removed before it can be used in the production of iron and steel. Magnetic separation is a common method employed to separate magnetic minerals from non-magnetic ones. Strong magnets, such as the Huate magnet separator, are used to attract and separate the iron ore particles from the gangue (unwanted materials). This step is critical for improving the purity of the ore.
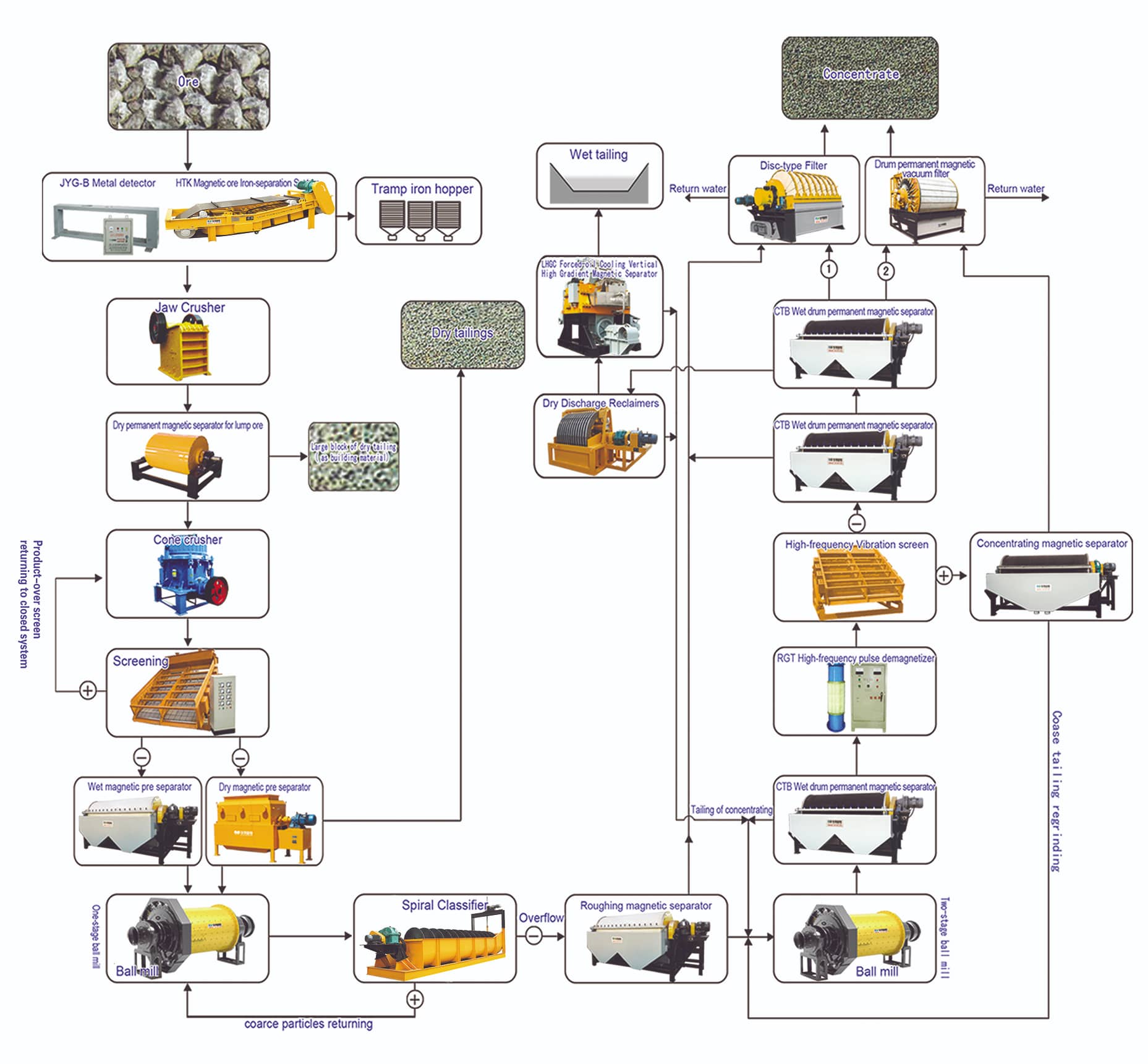
Beneficiation
The next step is the beneficiation of the ore, where the goal is to increase the iron content through various techniques. This process may involve washing, screening, and gravity separation methods to remove impurities and improve the quality of the ore. Beneficiation can also include flotation, where chemicals are added to the ore to make the iron particles float and separate from the rest of the material.
Pelletizing or Sintering
Once the ore has been beneficiated, it may be necessary to agglomerate the fine particles into larger ones for more efficient processing. Pelletizing involves forming small spherical pellets by tumbling the ore with additives such as limestone, bentonite, or dolomite. Sintering, on the other hand, involves heating the ore fines along with fluxes and coke breeze to form a semi-fused mass known as a sinter. These processes prepare the ore for the final extraction step by improving its physical properties and handling characteristics.
Smelting
The final step in the extraction process is smelting, where the iron ore is heated in a blast furnace along with coke (a carbonaceous fuel) and limestone (which acts as a flux). The intense heat breaks down the ore into molten iron, which collects at the bottom of the furnace, and slag, which floats on top and is removed. The molten iron is then cast into various shapes, such as ingots or billets, and further processed to obtain the desired iron and steel products.
It's important to note that different iron ore deposits and processing plants may have variations in the specific processes employed, but the overall principles remain similar. The extraction of iron from ore is a complex and multi-step process that requires careful management of resources and technology. The inclusion of advanced equipment like the Huate magnet separator enhances the efficiency and quality of the separation process, ensuring that the final product meets the required standards for iron and steel production.
Post time: Jul-08-2024